Your Test and Tag Experts 🏷️
Melbourne's Test and Tag Professionals
We offer on-site electrical testing and tagging of all your appliances & electrical devices to ensure that your business can operate safely, at ethical prices!
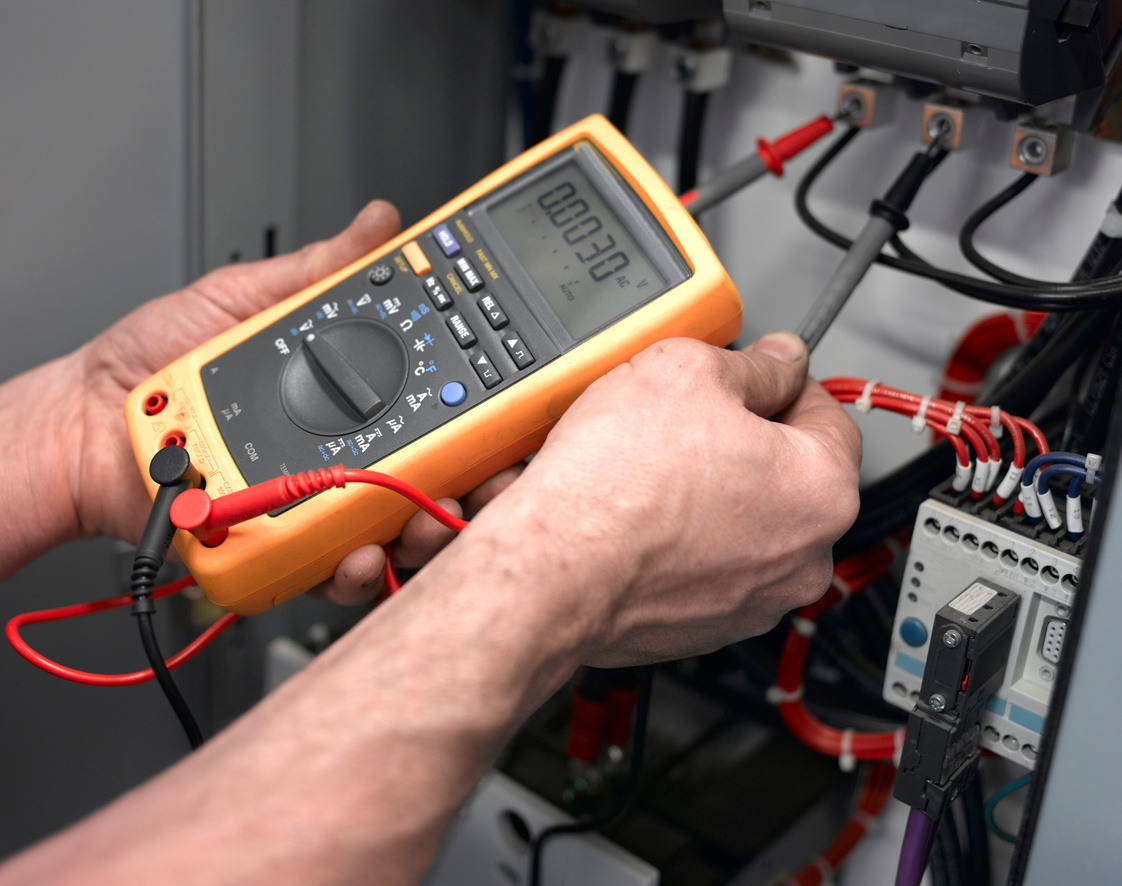
🏷️ All Test & Tag Services 🏷️
We test & tag the following:
⚡ 240v Appliances
⚡ 3 Phase Appliances
⚡ Portable Appliance Testing & Tagging
⚡ RCD Testing / Safety Switch Testing
⚡ Emergency Light Testing
⚡ Exit Light Testing
⚡ Residential Smoke Alarm Testing
⚡ Electrical Risk Assessment
⚡ And More!
We test & tag onsite at:
⚡ Offices
⚡ Workshops
⚡ Factories
⚡ Building Sites
⚡ Aged Care Facilities
⚡ Sporting Clubs
⚡ Child Care Centres
⚡ Trade Shows
⚡ Charity Organisations
⚡ Many Other Spaces!
Request a Callback
How Often Do I Have To Test? The "Standard" Guide
Determining the exact frequency for test and tagging can be flexible, allowing businesses to adjust timelines to meet their specific needs. At EPC Maintenance, we adhere to the recommended frequencies outlined by the standard. Here is the Standards testing schedule:
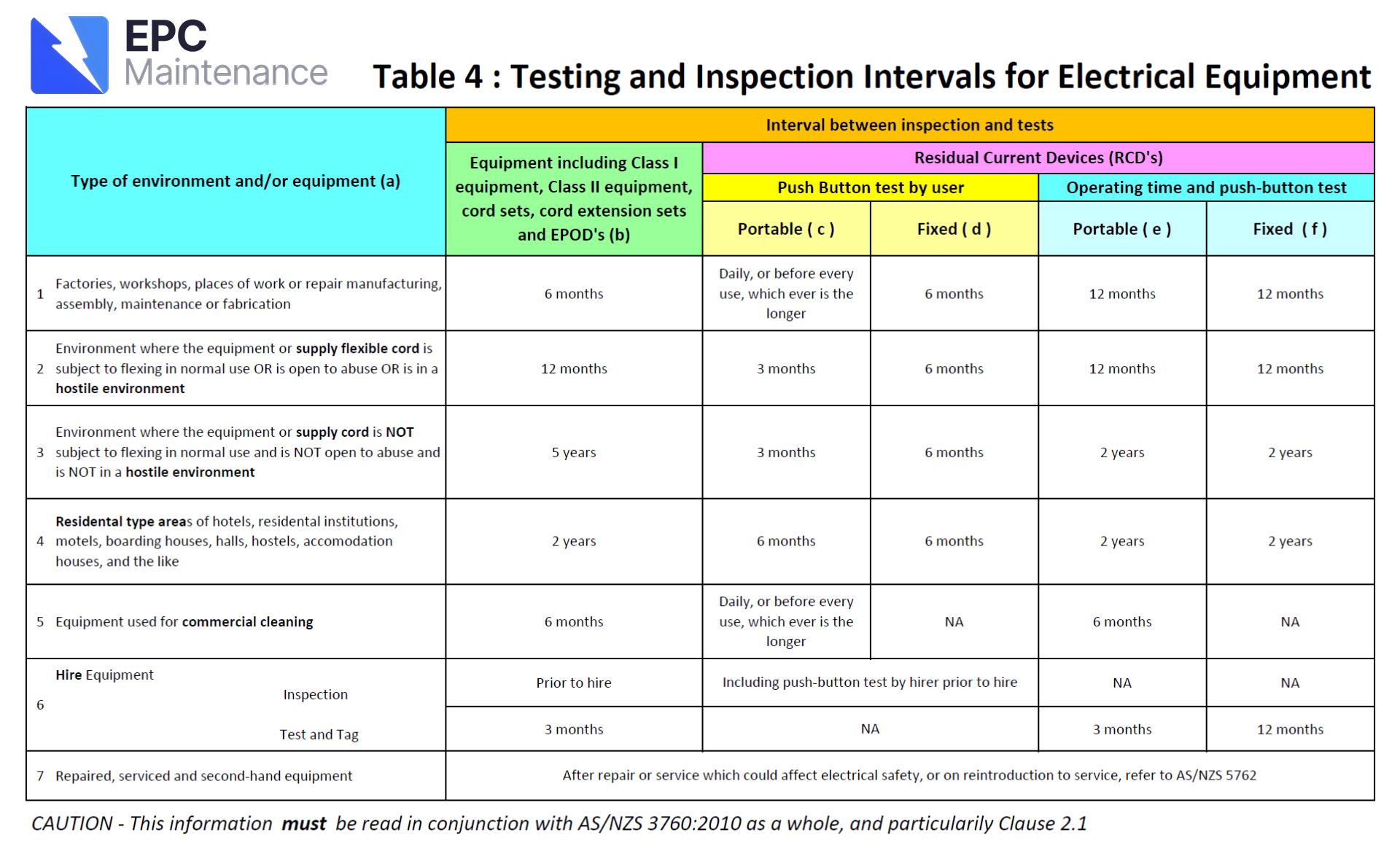
Test & Tag FAQ's
-
Electrical testing & tagging involves thoroughly checking the safety of electrical appliances. In Victoria, workplaces must demonstrate safe systems of work, including ensuring electrical safety.
Regular testing is essential for portable appliances such as power tools, extension leads, kitchen appliances & computers. The more frequently these devices are used, the higher the risk of wear & tear. Equipment used in harsher environments is particularly prone to becoming electrically unsafe over time.
By regularly testing and tagging your electrical equipment, you can maintain a safe workplace & prevent potential hazards. -
As an employer, it's your responsibility under the Occupational Health and Safety Act 2000 to provide a safe workplace for your employees.
No matter the size or type of your business, ensuring a safe working environment is crucial. Regular testing & tagging help you comply with Australian Standard AS/NZS 3760, ensuring your electronic equipment operates safely & effectively.
Neglecting this important step can lead to the failure of safety alarms & protections during an emergency, increasing the risk of electric shock or fire. At EPC, we offer peace of mind by inspecting, tagging & ensuring your workplace is properly protected. -
Any item that plugs into a wall socket or generator should be tested. This includes monitors, PCs, photocopiers & refrigerators. The environment in which the equipment is used will determine how often each item needs to be tested & tagged.
Newly purchased equipment doesn’t need immediate testing & tagging. Instead, it should have a "New to Service" tag applied & then be tested & tagged during the next scheduled service. -
At EPC Maintenance, we recommend the following testing frequencies based on common environments:
- Every 3 months: For building, construction, and demolition sites.
- Every 6 months: For factories, warehouses, and production facilities.
- Every 12 months: For workplaces where equipment or supply cords are subject to flexing or continual stress.
- Every 5 years: For environments where equipment or supply cords are not subject to flexing or continual stress.
These guidelines help ensure your equipment remains safe and compliant with regulations.
-
The Australian Standard provides guidelines on test & tag frequencies, inspections & record-keeping. Ensuring equipment in the workplace is safe is crucial to prevent accidents & avoid liability for employers & employees. According to the standard, each appliance must undergo the following tests:
- Visual Inspections
- Insulation Resistance
- Earth Continuity
- Polarity
- Earth Leakage
-
Along with proper testing methods, the standard also emphasises meticulous record-keeping for appliances:
- Tags on Each Item: Each tag should include the date of the test, the item tested, the person who performed the test, the test status & the next test due date.
- Comprehensive Records: Maintain a complete list of all tested items & their results.
- Faulty Items and Repairs: Document any faulty items & repair actions & share this information with the primary contact.
By following these recommendations, we ensure thorough tracking and maintenance of your appliances, keeping your workplace safe & compliant.
Ready To Get In Touch? Let Us Take Care Of Your Test and Tag
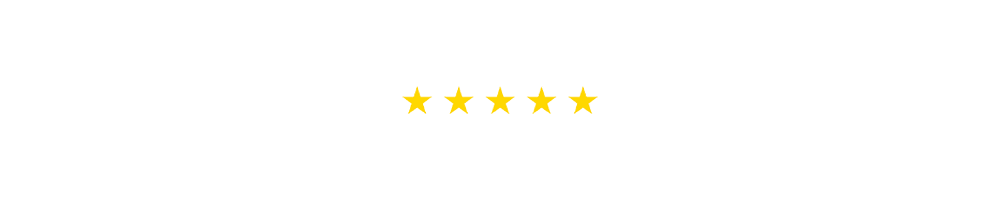
Jessica M. -
"EPC Maintenance did an outstanding job testing and tagging all our office equipment. Their team was professional, efficient, and thorough. Now we have peace of mind knowing everything is safe and compliant. Highly recommend!"
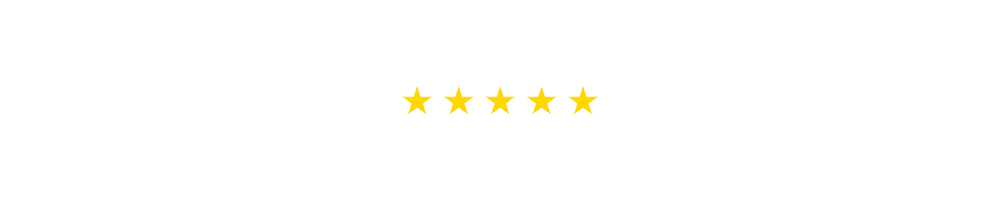
Dave K. -
"Fantastic service from EPC Maintenance! They were prompt, friendly, and extremely detailed in their work. Our factory equipment has never been safer. We’ll definitely be using their services again!"
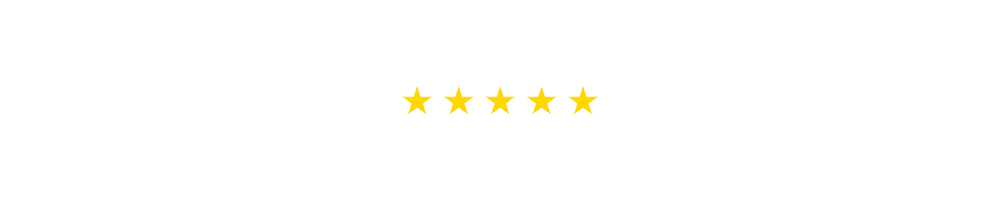
Linda S. -
"We had EPC Maintenance come in to test and tag our appliances, and they exceeded our expectations. They were knowledgeable and took care to explain the process. We feel much more secure with their tags on our equipment!"